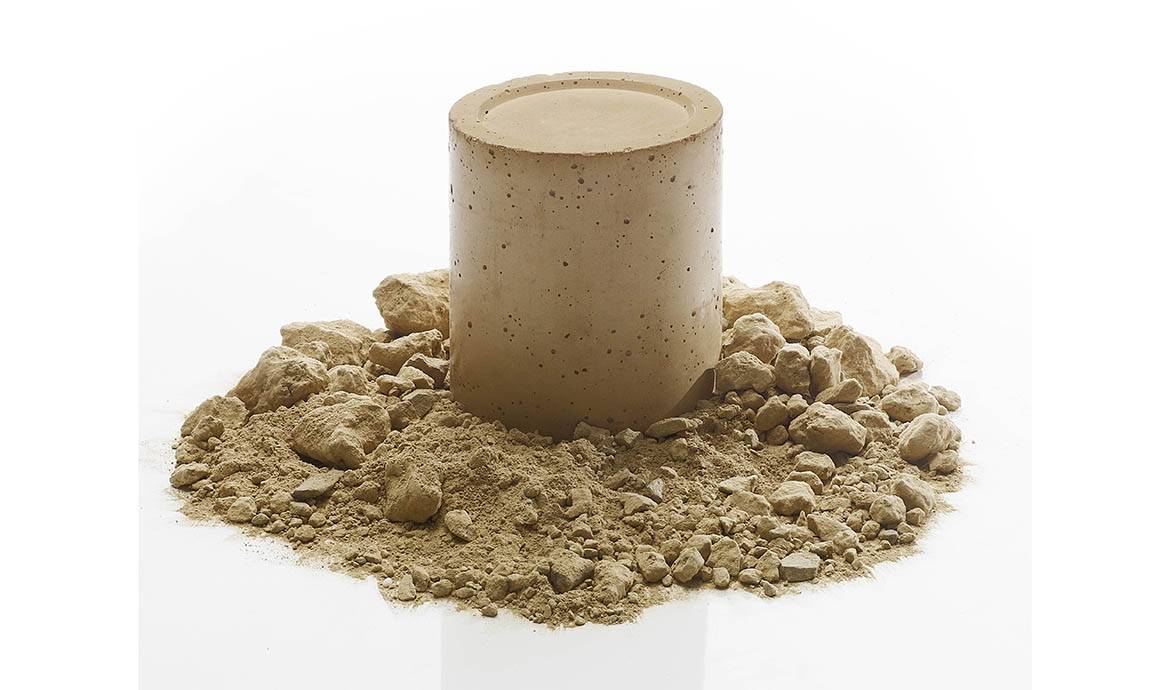
Deux Français ont mis au point une molécule, capable de produire un matériau aussi solide que le béton, mais moins polluant. Le tout made in France.
L'entreprise vendéenne a été sélectionnée en 2017 par le Grand Paris pour revaloriser les déblais du chantier de nouvelles lignes de métro à l'aide leur technologie HP2A.
L'histoire de cette technologie, capable de recréer de la pierre à partir de l'argile est surtout celle d'une rencontre. Entre David Hoffmann, ingénieur spécialisé dans la chimie des liants minéraux et Julien Blanchard, directeur d'Argilus, une entreprise fabriquant de l'enduit et des matériaux écologiques.
Ils sont partis d'un constat simple : le secteur de la construction représente 20% de la production de CO2 dans le monde et épuise le sable marin dans la mesure où le sable est nécessaire pour créer le béton.
“Pour fabriquer du ciment Portland, qui est utilisé dans 80% de la construction mondiale, il faut une quantité astronomique de sable. A ce rythme, 90% des plages à travers le monde auront disparu. Nous voulions créer une alternative. Une mutation nécessaire au regard des enjeux bioclimatiques mondiaux", explique Julien Blanchard.
En d'autres termes, avoir une empreinte environnementale allégée dans un monde où l'un des enjeux fondamentaux est la lutte contre le réchauffement climatique.
Le binôme commence alors à travailler sur une ébauche de procédés technologiques avant de parvenir, 10 mois plus tard, à la création de HP2A “High Performances Alcaline Activation” (“Haute performance activation alcaline” en VF).
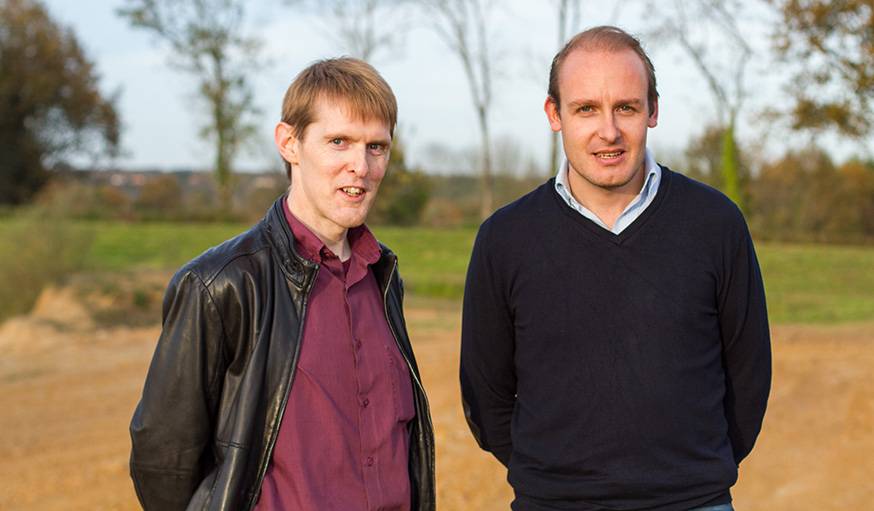
David Hoffmann et Julien Blanchard, créateurs de la technologie HP2A.
Récréer une pierre à partir d'argile.
Ainsi, David Hoffmann et Julien Blanchard entendent proposer un produit à l'impact environnemental très faible.
“Par notre procédé d'activation alcaline, la réaction moléculaire se fait à froid, ne nécessite aucun produit issu de la pétrochimie et est naturelle. Cette technologie, issue des géopolymères, revient à recréer de la pierre à partir de l'argile”, détaille le directeur d'Argilus.
Aucune combustion n'est donc nécessaire, contrairement au ciment classique, qui “lui, nécessite d'être chauffé à 1 300 degrés pendant de nombreuses heures. Pour produire une tonne de ciment, 900 kg de CO2 sont émis, contre 230 pour une tonne de HP2A.”
Autre argument en faveur de l'environnement selon Julien Blanchard, “l'argile est une matière première facile à extraire. De plus, grâce à l'activation alcaline nous pouvons utiliser des agrégats comme les sables non-marins (comme le sable du désert par exemple), ce qui est impossible pour le béton classique. Mais aussi des bétons broyés ou des agrégats végétaux comme le chanvre."
Un matériau recyclable.
Ce matériau est également recyclable jusqu'à 40 ans après son utilisation, en servant de liant pour fabriquer du béton.
Dernier avantage de ce ciment argileux ? Il ne se rétracte pas, contrairement à un ciment classique. Sa plus grande souplesse permettra de l'utiliser pour des constructions plus arrondies comme pour du mobilier urbain.
Mais ses applications pourront être bien plus nombreuses puisqu'il pourra servir pour les murs de fondations, ou encore la fabrication de colle ou de mortier, de quoi réjouir les particuliers désireux de construire plus durable.
La construction d'une usine pilote a débutée en Vendée, afin de commercialiser le HP2A au second trimestre 2017. Si pour le moment le binôme reste discret sur ses ambitions, ils envisagent d'ores et déjà une production de plusieurs milliers de tonnes.